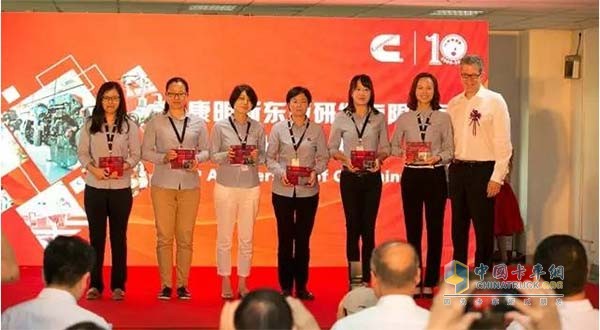
Cummins East Asia Technology R&D Center is Cummins’ 17th R&D institution in the world. After 10 years of development, Cummins has grown to become the second largest R&D base in the world outside of the US Technology Center. With a total investment of nearly US$100 million and a technical team of more than 300 people, a total of 24 test benches, including emission tests, have been put into use, as well as pilot centers, control laboratories, applied mechanics, materials science, chemical analysis, and cold start-ups. A large number of advanced testing and development platforms, including vibration and noise labs. Provide technical services including product design, verification and distribution, technology and product development, product support and product lifecycle management, and vehicle system integration.
Engine tested at R&D center
Cummins pays attention to localization development because the purpose of Cummins's R&D is to "develop the most appropriate technology is the key." Looking back at Cummings’ 40-year history in China, it can be divided into two major stages for the technological development process. In the first stage, Cummins introduced the mature technology platform in Europe and the United States directly into China, and realized localized production. In the second stage, Cummins aimed at the changes in the Chinese market, deeply understood the needs of Chinese customers, developed applicable power, and created a new platform. One of the most important carriers for achieving the second phase is the Cummins East Asia Research and Development Center. Since 2006, the R&D center has undertaken most of Cummins's local platform development and optimization in China. From engine to key components to power products, the product technology platform developed by East Asia R&D Center covers a wide range of automotive, construction machinery and Electricity and other markets. The most typical representatives of market-demand products that Cummins East Asia R&D Center is involved in include the heavy-duty engines such as Dongfeng Cummins's ISZ heavy-duty engine and the Futian Cummins ISG heavy-duty engine.
Cummins East Asia R&D Center is also an important force in China's emission reduction and environmental protection technologies. The engine test bench can support Euro V, Euro VI standards and off-road 3rd and 4th phase emission tests. The light, medium and heavy horse power benches can be used for emission certification in Europe, Russia, South Korea, Taiwan, Singapore, Australia and Brazil. Provide "passes" for Chinese OEMs to enter the international market. The Cummins East Asia Research and Development Center is dedicated to the development of power technologies that meet stringent emissions regulations and meet user performance requirements such as fuel economy. Since 2006, the R&D center has developed light, medium, and heavy-duty diesel engines for Cummins and joint ventures to meet the country's 3, 4, and 5 emissions, and it is also developing technical support for the National 6-vehicle diesel engine. At the same time, Cummins innovated and developed its own unique industrial power in China, providing tailor-made, unique power products for loaders, excavators, bulldozers and forklifts; and investing in the market to meet the country's low-cost, high-performance emissions. Natural gas products.
Technologists test engine performance
As the first Sino-foreign joint venture engine technology center in China, Cummins East Asia Research and Development Center is also the most critical carrier for research and development cooperation between Cummins and Dongfeng Motor and other Chinese partners. Including ISZ, ISG, and engineering machinery exclusive power L9.3 and other products, they all embody Cummins and its partners' technological innovation. The end-user demand-oriented technology development strategy, combined with global technological resources, enables East Asian R&D and Chinese OEM customers to correctly grasp the pulse of user needs, achieve high-efficiency and high-quality platform development, and lay a foundation for product market success. solid foundation. At the same time, Cummins East Asia Research and Development Center, as an important incubator for advanced engine technology, has also become an important force in promoting technological progress and industrial upgrading in China's related industries.
In addition to traditional diesel power, the R&D center also researches and develops related technologies and products including alternative fuel engines such as new energy, hybrid power, natural gas (CNG), and other forward-looking power technologies. At the same time, the R&D center is also committed to promoting Cummins’ advanced technology and development experience in China.
Plastic Chairs Making Machines
Meticulous division of labour, consecutive processes, professional of manufacture and high standard equipment ensure the high quality of the machine.
Factory introduced high precision maching tools, with the equipment of cutting machine tools, heattreating facilities, check out test sets and painting facilities, the processing ability for middle and large size machine, reach a high level in plastic industry while the quality if the machine is ensured at the same time.
The large size machine can produce different design of chairs.
Vertification of many year's market application, optimal combination configuration, stable, reliable and durable system with the characteristics of high efficiency, energy saving, low voice and strong power.
The strengthening design of template is carried out through multiple times of optimization design of major components such as template, based on the analysis of finite element software, which both guarantee the lifetime of template and protected mould.
High rigid template adopts the structure with coexistence of installation screw hole and T-shaped groove.
The tie rod of each machine model has passed the test by professional testing organization, which means that, the deflection of tie rod is within reasonable scope while guaranteeing the operation of machine.
Plastic Chairs Making Machines,Chair Making Injection Molding,Plastic Chair Making Machine,Safety Chair Molding Machine
Ningbo Tongyong Plastic Machinery Manufacturering Co. Ltd. , https://www.tongyong-machinery.com