First, the process description cement bag double seaming machine is a kind of automatic sewing machine, it controlled the industrial sewing machine and conveyor belt by computer, fully woven the two ends of the woven bag, and automatically cut the suture between the bags. Stack the bags neatly. It is an application of a highly efficient automatic industrial sewing machine. The workers put the woven bags one by one into the conveyor belt, and the sewing machine separates the bags at a set interval. At the same time, the sewing machine automatically folds and sews the woven bags at both ends.
Second, the working principle
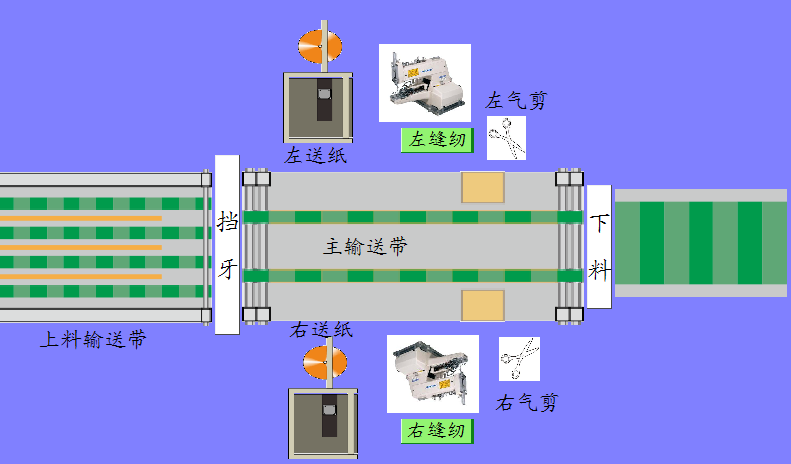
As shown in Figure 1, the cement bag double head seaming machine mainly includes several parts such as the feeding conveyor belt, the blocking tooth, the main conveyor belt, the cutting conveyor belt, the industrial sewing machine, the paper feeding machine, and the air shearing. Among them, the feeding conveyor belt, the main conveyor belt, and the industrial sewing machine are driven by the inverter, and they are required to have the same linear speed during operation. After the conveyor belt has been started, it has been running, and the woven bags are manually placed on the feeding conveyor by the workers. Pneumatic teeth separate the bags according to the spacing set on the touch screen. When the bag pitch is greater than the set spacing, the main conveyor and the sewing machine stop and wait for the woven bag on the feeding conveyor to reach the position of the teeth. The belt and sewing machine stop and continue to operate; when the pitch of the bag is less than the set spacing, the main conveyor and the sewing machine do not stop. Only in this way can high-efficiency production operations be guaranteed.
Third, sewing machine edge control program The electronic control system consists of a touch screen, PLC, four 1.5KW square V350 series inverter, teeth electromagnetic valve and other components. Through the touch screen, parameters such as bag width, bag spacing, and line speed can be set. In the previous working principle, we mentioned that the linear speed of each mechanism of the drive is the same during operation, so it can be based on the formula: line speed==Ï€*diameter*motor speed/gear ratio feeding conveyor belt main conveyor left sewing machine right sewing machine drawing two sewing Side machine electrical diagram PLC real-time calculation of the feeding conveyor frequency converter, the main conveyor inverter, the left sewing machine inverter, the right sewing machine inverter in the process of the target frequency, through the MODBUS communication control inverter speed. The main control difficulty of the system lies in the control of the teeth and the main conveyor frequency converter. It is necessary to accurately calculate the retraction and blocking time of the latch through the PLC timer, and also to control the operation of the main conveyor inverter. When the left-shield photoelectric and right-block electric light signal are blocked by the bag at the same time, the teeth are immediately retracted, and the main conveyor frequency converter advances or blocks the teeth for a certain period of time. Therefore, the response speed of the inverter is relatively high. In addition, the main conveyor belt is heavily loaded and requires a large torque at the start. The maximum operating line speed of the system is 30m/min. When the maximum operating speed is reached, the host inverter reaches 58Hz and the maximum current reaches 110% of the rated value. The excellent vector control performance of V350 inverter meets the special process requirements of the system.
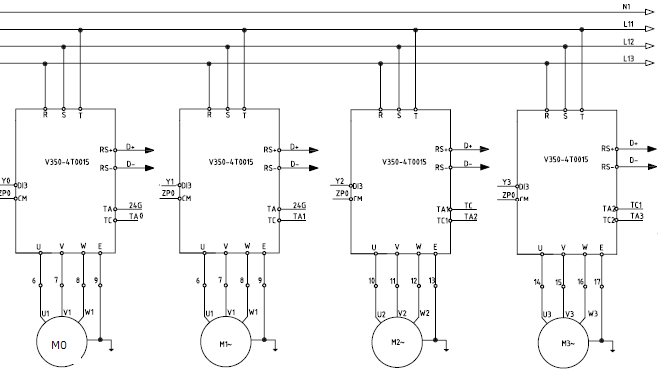
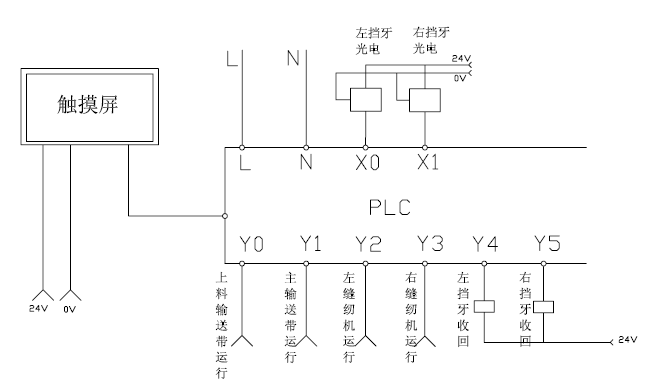
Fourth, system program advantages:
(1) Running the inverter with the external terminal given way can accurately control the running time of the main conveyor belt. If the inverter is operated by communication, the MODBUS communication may interfere and affect the separation between the bags.
(2) The host inverter has large starting torque, strong overload capacity, and long-term operation under 110% overload. At the same time, the production speed is increased and the efficiency is improved.
(3) The host inverter has a short acceleration and deceleration time, a fast response speed, and precise spacing between bags.
(4) The inverter has high speed stability accuracy, and the speed of the entire line is required to be the same during operation. If the speed accuracy is low, the needle of the sewing machine may be easily broken.
(5) Low failure rate and easy maintenance. V. Summary The system controls the feeding conveyor, the left sewing machine, the right sewing machine, the bag-receiving part and the paper-feeding part. The difficulty lies in the control of the teeth and the main conveyor. The performance of the V350 series inverters plays a key role in the control of the host, improving the production speed and efficiency. This control scheme has been widely used in sewing machines.
Second, the working principle
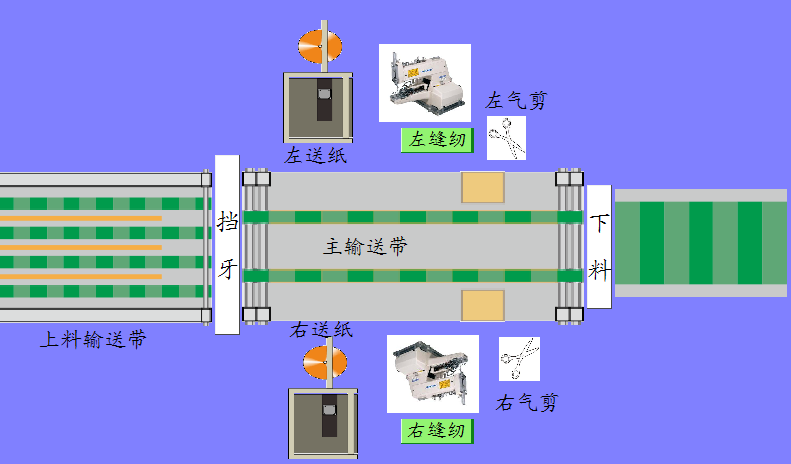
Figure 1 Slot machine schematic
As shown in Figure 1, the cement bag double head seaming machine mainly includes several parts such as the feeding conveyor belt, the blocking tooth, the main conveyor belt, the cutting conveyor belt, the industrial sewing machine, the paper feeding machine, and the air shearing. Among them, the feeding conveyor belt, the main conveyor belt, and the industrial sewing machine are driven by the inverter, and they are required to have the same linear speed during operation. After the conveyor belt has been started, it has been running, and the woven bags are manually placed on the feeding conveyor by the workers. Pneumatic teeth separate the bags according to the spacing set on the touch screen. When the bag pitch is greater than the set spacing, the main conveyor and the sewing machine stop and wait for the woven bag on the feeding conveyor to reach the position of the teeth. The belt and sewing machine stop and continue to operate; when the pitch of the bag is less than the set spacing, the main conveyor and the sewing machine do not stop. Only in this way can high-efficiency production operations be guaranteed.
Third, sewing machine edge control program The electronic control system consists of a touch screen, PLC, four 1.5KW square V350 series inverter, teeth electromagnetic valve and other components. Through the touch screen, parameters such as bag width, bag spacing, and line speed can be set. In the previous working principle, we mentioned that the linear speed of each mechanism of the drive is the same during operation, so it can be based on the formula: line speed==Ï€*diameter*motor speed/gear ratio feeding conveyor belt main conveyor left sewing machine right sewing machine drawing two sewing Side machine electrical diagram PLC real-time calculation of the feeding conveyor frequency converter, the main conveyor inverter, the left sewing machine inverter, the right sewing machine inverter in the process of the target frequency, through the MODBUS communication control inverter speed. The main control difficulty of the system lies in the control of the teeth and the main conveyor frequency converter. It is necessary to accurately calculate the retraction and blocking time of the latch through the PLC timer, and also to control the operation of the main conveyor inverter. When the left-shield photoelectric and right-block electric light signal are blocked by the bag at the same time, the teeth are immediately retracted, and the main conveyor frequency converter advances or blocks the teeth for a certain period of time. Therefore, the response speed of the inverter is relatively high. In addition, the main conveyor belt is heavily loaded and requires a large torque at the start. The maximum operating line speed of the system is 30m/min. When the maximum operating speed is reached, the host inverter reaches 58Hz and the maximum current reaches 110% of the rated value. The excellent vector control performance of V350 inverter meets the special process requirements of the system.
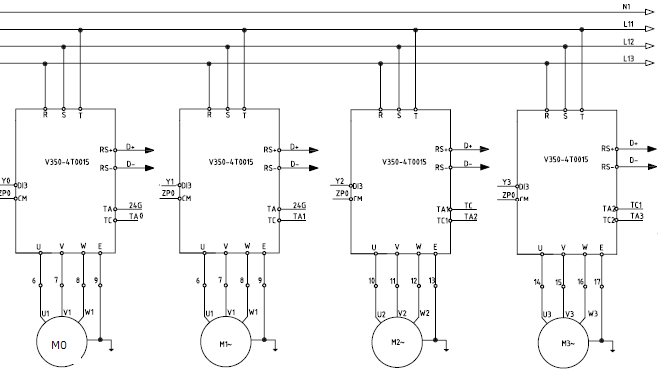
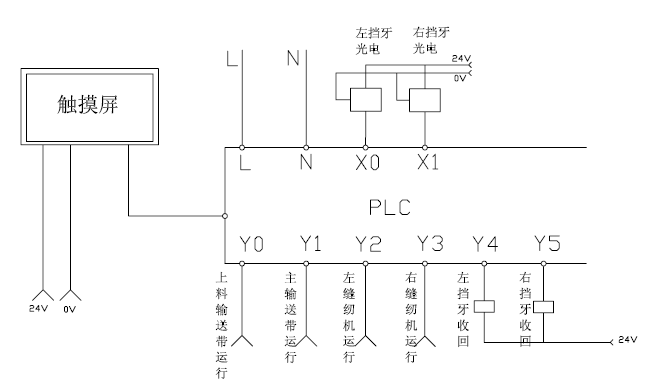
Figure 2 Electrical diagram of sewing machine
Fourth, system program advantages:
(1) Running the inverter with the external terminal given way can accurately control the running time of the main conveyor belt. If the inverter is operated by communication, the MODBUS communication may interfere and affect the separation between the bags.
(2) The host inverter has large starting torque, strong overload capacity, and long-term operation under 110% overload. At the same time, the production speed is increased and the efficiency is improved.
(3) The host inverter has a short acceleration and deceleration time, a fast response speed, and precise spacing between bags.
(4) The inverter has high speed stability accuracy, and the speed of the entire line is required to be the same during operation. If the speed accuracy is low, the needle of the sewing machine may be easily broken.
(5) Low failure rate and easy maintenance. V. Summary The system controls the feeding conveyor, the left sewing machine, the right sewing machine, the bag-receiving part and the paper-feeding part. The difficulty lies in the control of the teeth and the main conveyor. The performance of the V350 series inverters plays a key role in the control of the host, improving the production speed and efficiency. This control scheme has been widely used in sewing machines.
Ac Fan,Ac Table Fan,Condenser Fan,Rechargeable Air Cooler
Kennede Electronics MFG. Co., Ltd. , https://www.jmkennede.com